What is Kaizen and what is it not?
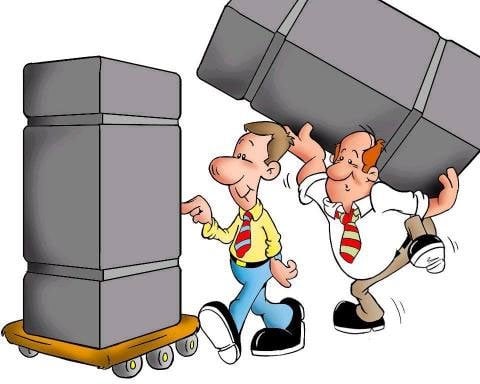
In addition to the significant contribution of management to the development of factories, it is obvious that numerous improvements ("Kaizens") made by encouraging the creativity of all employees will make a significant contribution to our products, production processes and therefore to our competitive power.
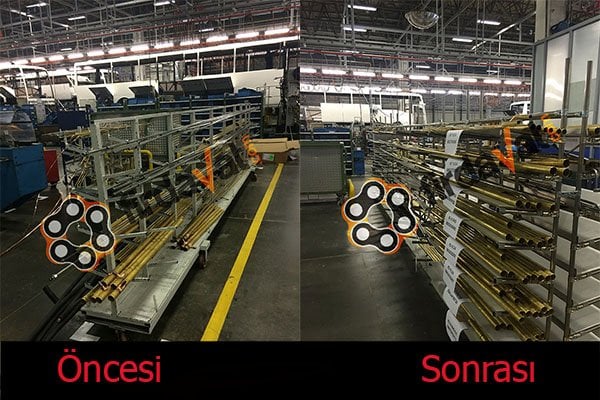
In Japanese, Kai means "change" and Zen means "good, better". In its entirety, Kaizen is a Japanese word meaning "CONTINUOUS IMPROVEMENT". The main idea of Kaizen is to find and implement continuous small improvements in one's environment and areas of responsibility, either as a team or individually.
Innovation is a completely different matter, it is a radical change in the current situation as a result of major changes and/or investments in new technology and/or tools, and this is not Kaizen.
Dynamic Shelving Products Review Video
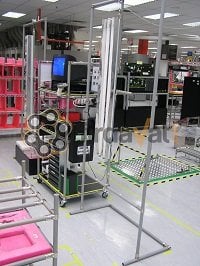
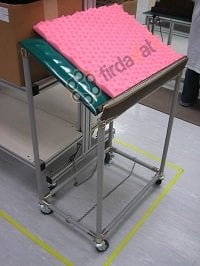
For Kaizen, it is essential not to be satisfied with the current conditions and standards that have already been achieved, to seek innovations, to be proud of the improvements made and to appreciate them. The beginning of improvement is to recognize the need for improvement. The need arises when a problem or inadequate standards are recognized. Those who need to recognize these problems are the ones who do the work themselves. If there is no problem that is recognized, there is no need for improvement, therefore the necessary atmosphere for Kaizen cannot be created.
Who Performs Kaizens?
Kaizen covers all employees in a factory. By encouraging employees, it is possible for individuals to do many Kaizens and get effective results, and this is very important. On the other hand, in medium-sized and larger factories, team work can be done by people with different responsibilities due to the division of labor, using problem-solving techniques. Problem-solving techniques are also used intensively in these team works. Methodical improvement studies carried out by teams are called "Kobetsu Kaizen"..>> Click for more..
Related Subcategories