Kaizen ve 5S
Kaizen Nedir? Ne değildir?
Fabrikaların gelişiminde yönetimin önemli katkısının yanısıra, tüm çalışanların yaratıcılığının teşviki ile yapılan çok sayıda iyileşmenin ("Kaizen`lerin) ürünlerimize, üretim süreçlerimize, dolayısı ile rekabet gücümüze önemli katkı getireceği aşikardır.
Japonca`da Kai: "değişim", Zen: "iyi, daha iyi" anlamına gelen sözcüklerdir. Bütününde Kaizen "SÜREKLİ İYİLEŞTİRME" anlamını taşıyan Japonca bir sözcüktür. Kaizenlerin ana fikri ekip veya bireysel olarak, insanın çevresinde ve sorumlu olduğu alanlarda sürekli küçük iyileşmeleri bulması ve uygulamasıdır.
Yenilik (inovasyon) tamamen farklı bir şekilde, yeni teknoloji ve/veya araçlarda yapılan büyük değişiklikler ve/veya yatırımlar sonucu mevcut durumun köklü biçimde sıçrayarak değiştirilmesidir ve bu konu Kaizen değildir.
Kaizenler için mevcut koşullarla, zaten ulaşılmış olan standardlar ile yetinilmemesi, yeniliklerin aranması, yapılan iyileştirmelerle gurur duyulması ve takdir edilmesi şarttır. İyileştirme için başlangıç, iyileştirmeye olan ihtiyacın fark edilmesidir. İhtiyaç bir problemin ya da yetersiz standardın fark edilmesiyle ortaya çıkar. Bu problemleri farketmesi gerekenler ise işi bizzat yapanlardır. Fark edilen bir problem yoksa, iyileştirmeye ihtiyaç doğmaz, dolayısı ile Kaizen yapılması için gerekli atmosfer oluşamaz.
Kaizenler Kimler Tarafından Yapılır?
Kaizen bir fabrikadaki tüm çalışanları kapsar. Çalışanların özendirilmesi ile bireyler tarafından birçok Kaizen yapılması, etkin sonuçlar alınması mümkün olur ve bu çok önemlidir. Diğer taraftan orta ölçek ve üzeri boyuttaki fabrikalarda iş bölümü nedeniyle değişik sorumluluklardaki kişiler tarafından problem çözme tekniklerinin de kullanımı ile ekip çalışmaları da yapılabilir. Bu ekip çalışmalarında problem çözme teknikleri de yoğun olarak kullanılır. Ekipler tarafından yapılan metodik iyileştirme çalışmalarına "Kobetsu Kaizen" denir.
Kaizenler Hangi Alanlarda Yapılabilir?
Kaizen işyerlerinde ürünlere ve üretim proseslerine yönelik olarak, ofiste, evde, hastanede, kısaca her yerde ve her zaman uygulanabilir. Özellikle Japonya`da Kaizen yaşamın her alanında uygulanmaktadır. Fabrikalarda Japonca "Muda" denilen 16 büyük kaybın sıfıra indirilmesi hedefi doğrultusunda yapılacak Kaizenler ile verimliliğin arttırılabileceği gibi ürün ve üretim maliyetlerinde de kayda değer düşüşler sağlanabilir.
Nitekim, KAİZEN uygulamaları yapılan birçok fabrikada çalışanlar yaratıcılıklarını geliştirmişler, yarattıkları yenilikleri kullanmışlar ve makinalarını, çalışma alanlarını, ürünlerini sürekli geliştirerek diğer firmalar tarafından izlenen öncü konumuna yükselmişlerdir. Fabrika çalışanları tarafından yapılan sunuşlara katılan izleyicilerin olumlu izlenimleri bu gelişimin göstergesi olmuştur.
Günümüz rekabet ortamında, girdilerin ürün haline dönüşürken hangi sürecin ne kadar iyi yürütüldüğü çok önem taşır. Çünkü müşteriler, sanayi ürününü taşıdığı "Kalite, maliyet, teslim süresi" olarak bilinen "değer kriterleri" ürünün bedeli ile karşılaştırıp satın alırlar.
QCD: kalite, maliyet ve teslim süresi kelimelerinin İngilizce baş harfleridir.
`Üreticilerin, ürünlerini daha çok satabilmeleri için çıktılardaki değer kriterlerini arttırması gerekir. Bu artış ürün tasarımı, üretim süreçleri (prosesleri) ve 5M faktörleri gözönüne alınarak mümkün olabilir.
Müşteri açısından yaratılan fark rekabeti belirler. Bu sebeple, fark iyileşmede, hızlı iyileşmede ve müşterinin değer kriterlerini daha çok tatmin ederek rekabet gücü elde etmededir.
Japonca`da "Kai" ve "Zen" sözcüklerinden oluşan Kaizen "SÜREKLİ İYİLEŞTİRME" anlamını taşır. Kaizenlerin ana fikri ekip veya bireysel olarak, insanın çevresinde, sorumlu olduğu alanlarda sürekli küçük iyileşmeleri bulması ve uygulamasıdır.
Sanayide, süreçlerin yanı sıra çıktılar da fark yaratmada önem taşır. Bunlar, kalite-maliyet-teslim süresi de dikkate alınarak üretilen çıktılardır. Hergün yapılan Kaizen faaliyetleri ile önemli ölçüde endüstri süreçlerini iyileştirmek mümkündür. Dolayısıyla, maliyetler düşer, kalite artar ve teslim süresi kısalır. Bu nedenle, Kaizen, süreçlerdeki küçük iyileşmeler ile çıktılardaki değer kriterlerini geliştiren faaliyetlerdir.
Japon Human Resources tarafından tanımlanan şekliyle Kaizen, bir amaç doğrultusunda iyileşmeler bütünü veya kullanılan bir metodun değiştirilmesidir. Diğer bir tanım, küçük değişikliklerin birikimiyle yapılan iyileşmelerdir. Dolayısıyla Kaizen herkesin yapabileceği, o gün yaptığı! işi en iyi bilen ve tezgahın başında çalışan kişi tarafından yapılabilecek iyileşmeler ve bunların çok sayıda yapılarak sürekli kılınmasıdır.
Sanayi açısından Kaizen, bir amaç doğrultusunda üretim metodunda -süreç ya da süreçlerinde- ürün özelliklerinde küçük değişiklikler yapılarak çıktılarda sağlanan iyileşmelerdir.
Örneğin, konfeksiyon sanayiinde çalışan bir operatörün yaptığı bir iyileşme bir zaman tasarrufu sağlayabilir. Operatörün kendi sürecinde, süreçlerinde, yani üretim metodunda veya üretilen ürünlerde yaptığı küçük iyileşme bir Kaizendir.
Kaizenler ürün özelliklerinde de yapılabilir.
Ağırlıklı olarak, süreçlere yapılan Kaizenler daha etkilidir. Süreçler bir üretimde çok tekrarlandığında yüzlerce, binlerce defa tekrar edilen bir işlemde küçük iyileşmelerin toplamı ile yüksek bir iyileşme seviyesi elde edilebilir.
Örneğin bir operatörün yaptığı kaizen ile kendi sürecinde %7`lik bir iyileştirme yaptığını varsayalım. Bu durumda 1000 adetlik bir üretim partisinde 70 parçalık fazla ürün elde edebilir.
Kaizenler mütevazı, mevcut bütçeyle, mevcut personelle, mevcut donanım ve makinalarla yapılabilir.
Öncelikle, bireysel fikirler ve çalışmalar ile bir metodun iyileştirilmesi diye tanımladığımız önce-sonra "Kaizen"lerinden bahsedelim. En basit örnek şöyle olabilir: Örneğin, bir tezgahta, biri kısa boylu, diğeri uzun boylu iki kişinin beraber çalıştıklarını varsayalım. Çalışanlardan biri, bir Kaizen yapabilir: Kısa boylu olanın ayağının altına bir platform koyarak, kendini yükseltmesi sağlanabilir. Böylece sürece yönelik bir iyileşme sağlanır, işler daha kolay yapılabilir, sonuçta da verim artmış olur.
Önce: Bir metal parçanın çapaklarının temizlendiği çalışma ortamını düşünelim. Masanın üstü metal tozlar ile dolu, bunlar yere dökülüyor, zaman zaman yere dökülüyor, sonra temizleniyor. Tabii boşuna emek, boşuna kayıp…
Sonra: Çalışan üç Kaizen yapabilir: Önce masasının kenarına bir siperlik yaparak tozların yere dökülmesini önlüyor; böylece yeri önce kirletip, sonra boşuna temizlemekten kurtuluyor. Bunu takiben ikinci kaizen: Masaya bir delik delsek , altına talaş kutusu koysak, masanın üzerinden sık sık talaş temizlemekten daha kolay değil mi? Talaş kutusunu sadece dolunca dökmek gerekebilir. Üçüncü Kaizen: Talaş kutusunu niçin masanın altına eğilip alalım ve elle taşıyalım? Onun yerine talaş kutusunun altına tekerlekli bir araba koysak, dolunca istediğimiz yere çekerek kolayca götürebiliriz.
Lastik balans makinasının açma-kapama düğmesi çok kullanıldığından bozulmuştur. Operatör yapıştırdığı bir bant ile hem açma-kapama düğmesinin kopan parçasını yerine tutturmuş hem de sürekli kirlenmeyi önlemiş olmaktadır. Zaman zaman kirlenen bant parçası değiştirilmektedir.
KAİZEN NASIL YAPILIR?
İyileştirme yapmak için önce problem tanımlanır, sonra fikir üretilir ve çözüm önerileri belirlenir. Son olarak da öneriler uygulanır. Uygulanmayan fikir hiçbir anlam taşımaz, yani iyileşme gerçekleşmemiş olur.
Sorunu tanımlama aşamasında; "Halen yapılmakta olan en iyidir" diye düşünülürse yapılanı iyileştirmek mümkün olmayabilir.
Problem bulma yöntemleri
Birinci metod; sorunlar, hatalar, yanlışlar ve sıkıntı gibi görülebilir problemleri farketmektir. Örneğin, bir çalışan "bugün makinelerin sesi daha farklı" diye düşünebilir. Eğer bir makinenin sesi değiştiyse, problem geliyor demektir. Problemi o çalışan hisseder, bu durumu ustabaşına, şefine, amirine, atölye şefine ya da müdürüne bildirir. Bu gibi durumları sezebilen çalışanlar Kaizenler sisteminin içinde liderlik görevi de üstlenebilirler.
Bir de görünmez sorunlar vardır. Süreçlerde sorun görünmese de, birtakım kayıplar olabilir.
Kitabın sonunda, bu sorunları tanımak için kullanabilen, Japonların `muda` diye adlandırdığı 16 büyük kayıp listelenmiştir. Bunlar, ekipman verimsizleştiren 8 kayıp, işgücü verimini düşüren 5 kayıp, malzeme ve enerji kayıplarıdır. Bu 16 kayıp, fabrikalarda oluşan kayıplardır. Dolayısıyla, ister mühendislik ofisleri olsun, ister yöneticiler olsun, ister çalışanlar olsun,
bu 16 kayıba odaklanılırsa, kayıpları azaltacak birçok Kaizen yapılabilir. Görünmeyen sorunların arasında, hareketlerin israfı, 16 kayıbın arasında lojistik olarak bulunur. Hat organizasyonunun hatalarının içinde de kısmen geçen kayıplar vardır. Ekipmanlar konusunda da, hız kaybı benzer bir kayıptır.
Bu problemleri bulmak, lokalize etmek için, `neden`, `ne oldu` gibi birtakım anahtar kelimelerle düşünmek gerekir. "Her zaman bu şöyledir." "Niçin öyle? Ben onu öyle istemiyorum, daha iyi olabilir." "Burada birşey ters gidiyor" gibi düşüncelerin herbiri, aslında iyileştirmeler için birer veridir. Sadece belirli kişilerin iyileştirmeleri yapabileceğini düşünmek yerine bu durumu sorgulamalı ve işletmede gereken iyileştirmeyi yapacak diğer çalışanların da olabileceği hatırlanmalıdır. O nedenle bu anahtar kelimeler, bu düşünce mantığını tetikleyen kelimelerdir.
İkinci aşama: Fikir üretme. Problemi çözmek için fikir üretmek gerekir. Fikir üretilirken Kaizenler, eleme, azaltma ve değiştirme yöntemiyle tetiklenir. Lüzumsuz olan elenebilir. Gereğinden fazla olan azaltılarak Kaizen yapılabilir. Bunlar ürünlerdeki çıktıları azaltan iyileştirmelerdir. Ya da değiştirerek de Kaizen yapılabilir. Dolayısıyla, bu üç alanda fikir üretilebilir.
"Değiştirerek Kaizen" yapmayı açıklamak için bir başka örnek, fabrikalardaki kontrol panolarının soğutma fanlarıdır. Fabrikanın elektrik panosundaki fanların arızalanması, çoğunlukla cihazların da arızalanmasına yol açar. Bu yüzden fanların çalıştığından emin olmak gerekir. Tek yöntem fan sesini dinlemek değildir. Aşağıda görülen metod birçok fabrikada uygulanan pratik bir metoddur. Fanların ızgaralarına birer kurdele bağlanır, fanlar çalıştıkça kurdeleler dalgalanacağı için fanların çalışıp çalışmadığı uzaktan bile kolayca anlaşılabilir. Kurdelelerin havalanmaması, fanların çalışmadığını ve değiştirilmesi gerektiğini gösterir.
Atölyenin köşesinde duran kompresör atölye içindeki havayı alarak kendisini soğutmakta ve oluşan ılık hava gökyüzüne bir kanal vasıtasıyla atılmaktadır. Civarda kapı da açıldığında kışın çalışanlar bazen üşümekte ve bu noktaya elektrikli ısıtıcılar koyulmasını önermektedirler. Fabrikanın bakımcısı bir Kaizen yaparak dışarı giden sıcak havanın yolunu bir sac parçasıyla kapatmış, sıcak hava kanalının yanından atölyeye doğru bir delik açmıştır. Böylece boşa giden sıcak hava atölyenin ısıtmasında kullanıldığından çalışanların ısınma ihtiyacını sağlar hale gelmiştir. Yazın atölyeye açılan delik kapatılarak kanalın ağzını tıkayan sac parçası çıkartılacak ve sıcak hava yine dışarıya atılacaktır. Böylece işletmenin yaklaşık 3000 kcal/saat ekstra enerji satınalmasına gerek kalmamıştır.
5S KAİZEN
Çalışma ortamında topyekün mükemmelleşme isteniyorsa, fabrika ve atölye düzeni 5S Kaizenleri ile metodlu bir şekilde iyileştirilebilir. `5S Kaizen` kişi ve/veya grup aktiviteleriyle çalışma ortamının iyileştirilmesidir.
Düzenli fabrika ve atölyelerde, takımlar ve aletler yerlerinde durur, aletlerin durduğu yerin hemen yanında makina vardır. Yer döşemesi eski olsa bile temizdir, kırpıntıların, talaşların, hurdaların biriktirildiği ayrı kovalar, kutular vardır. Böyle fabrikalarda verim yüksektir, maliyetler düşüktür, fireler az ve kontrol altındadır, ürünlerdeki hatalar azdır.
Bazen de böylesi düzen fabrikaların tüm atölyelerinde olmayabilir. Bir atölye diğerlerinden düzensiz, verimsiz olabilir ve iş akışını bozacak, yavaşlatacak şekilde kalitesiz bir çalışma ortamı olabilir. Düzensiz ortam sebebiyle iş akışında aksaklık yaşamak yüksek bir olasılıktır. Kayıt tutulmayan ve ölçülemeyen birçok aksaklık, çalışma ortamının kötülüğünden kaynaklanır.
Metodoloji Japonya`dan yayıldığı ve artık bu kelimeler sembol halini aldığı için, bu 5S de Japonca kelimelerin -seiri, seiton, seiso, seiketsu, shitsuke- kelimelerinin baş harflerinden oluşmaktadır 5S, toparlanma, düzen, temizlik, standardizasyon, disiplin yada oto kontrol kelimelerinden oluşur.
Burada, toparlanma, düzen, temizlik, standardizasyon, disiplin konusunu aşama aşama iyileştirmek yani Kaizen yapmak mümkündür.
55 Kaizenlerin ilk evresi `seiri` yani toparlanmadır çalışma bölgesinde ilk yapılacak şey, 5S Kaizenlerde toparlanmadır.
Öncelikle üretimde gerekli ve gereksiz olanlan belirlemek, ayırt etmek ve gereksizleri temizlemekten başlanabilir. Üretim süreçlerinde kullanılmayan bir malzeme, alet veya aparatlar çalışma ortamında bulundurulmamalıdır.
Toparlanma aşamasında, başlangıçta dağınık yerin bir fotoğrafını çekmek önerilir, böylece farklılık gözlemlenebilir ve farkındalık yaratılabilir. Önce ve sonrası arasındaki farkı gösterip, çalışanlar ile yapılan iyileştirmenin gururunu paylaşmak,
Kaizen`in yaygınlaşması için önemli bir motivasyon aracı olarak kullanılabilir.
Yine Japon üreticilerin kullandığı pratik bir yöntemde operatör, ayın birinde işbaşı yaptığında çalıştığı ortamdaki çeliklerin, takımların, makinanın, etraftaki bütün malzeme ve ekipmanın üzerine kırmızı bir etiket yapıştırır. Ay içinde kullandığı malzemenin, aletin, aparatın üstündeki etiketi çöpe atar. Ay sonunda üzerinde hala kırmızı etiket olan malzemeleri, aletleri kontrol eder; böylece bir ay süreyle hangi malzemeyi, kullanmadığını belirler. Çoğu zaman çalışanlar, bu alet veya aparatların aslında orada olduğunun bile farkında değillerdir. Bir ay boyunca kullanılmayan cihaz bir başkasına ya da başka bir operasyonda kullanılmak üzere başka bir birime de verilebilir.
Bu şekildeki lüzumsuz ve az kullanılan malzeme, alet veya aparatlar ortaya çıkar, tesbit edilmiş olur. Bu tesbitten sonra onu depoya kaldırmaya, iade etmeye, satmaya, hurdaya atılacaksa atmaya karar vererek, çalışma ortamından uzaklaştırır. Böylece çalışma ortamı genişler ve uzun vadeli bakıldığında, aynı metrekarede daha çok üretim yapılabilir. Etrafta daha az malzeme olduğu için seçim ve malzemeye ulaşmak dana kolay olur. Sonuç verim artışıdır.
İkinci faaliyet ‘seiton’ düzenli olmaktır. Takımları düzenli bir şekilde istiflemek, bunların kaybolmasına engel olmaktır. Toparlanma - seiri - ile düzenli olmak - seiton-birbirini tamamlarlar. Önce kırmızı etiket süreci ile lüzumsuzlar ayıklanır, sonra düzenlenir ve böylece kolaylıkla daha iyi bir işyerine ulaşılabilir.
Bir üretim noktasında lazım olabilecek alet veya aparatı en geç 30 saniyede
bulabilmek işi aksatmadan verimli şekilde yapabilmenin gereğidir. `30 saniye prensibi`ne göre kullanılacak olan malzemeyi bulmak için 30 saniyeden fazla zaman ayırmamak gerekir. Örneğin, kalıp değiştirme operasyonlarında bu sorun çok görülür. Bir yerde bir plastik enjeksiyon presi veya eksantrik pres vardır ve ona kalıp bağlanacaktır. Kalıp getirilir. Kalıbı tablaya bağlayan cıvatalar için önce 23 numara anahtar gerekir. 23 numara anahtar bulunup getirilir, civata bağlanır. Ama aynı iş için bir de 18 numara anahtar gereklidir, fakat bu anahtar yerinde yoktur. Bu yüzden kalıp bağlama dolayısı ile operasyonunun "set-up" süresi uzar; pres daha uzun süre bloke olur, durur ve üretimde kayıp meydana gelir.
Bir anahtar kayıpsa ya da eksikse, bunun en baştan, yani kalıp bağlama operasyonundan önce farkedilmiş olması gerekir. Resimdeki sistem sayesinde, aletler yerlerinde muhafaza edilerek bu sağlanabilir. Önemli olan, bir iş için kullanılacak olan gereci en fazla 30 saniyede bulabilmesidir. Bu da 5S aktivitelerinin temel hedeflerinden biridir.
Dolayısıyla, bu arama-bulma operasyonlarının çok pratik bir şekilde gerçekleşmesi gerekir. Örnek verecek olursak el aletlerinin asılı olduğu panolarda her aletin yerinin belli ve çizili olması alma, geri koyma, eksik aletlerin kaybolmadan belirlenip aranabilmesi için önemli fayda sağlar.
Sonuçta, yerleşim dizaynında daha fonksiyonel davranarak ve tanımlı parçalar ile çalışarak iyileşme sağlanabilir.
Muntazam istifin getirdiği, arandığı zaman aranan malzemelerin bulunmasının kolaylığı ve yararı yadsınamaz. Bu tür kayıpları ortadan kaldırmak için "seiton" aktiviteleri ve malzemelere, hammaddeler ayrılmış, etrafı çizgi ile belirlenmiş yerler çok önemli ve gereklidir.
Düzende, prensip olarak, rafın üzerindeki sembollerle parçaların üzerindeki sembollerin tutarlı olması önemli bir vakit kazandırıcı faktördür. Malzemelerin tiplerine göre tasnifi ve bu malzemelerin bulunduğu kutulann yerlerinin belli olması gerekir.
Bu açıdan faydalı bir yöntem de bir malzeme kutusunun üzerindeki yazı ile, raf üzerindeki yazının aynı olmasıdır. Böylelikle, yerleştirme ve bulmada önemli kolaylıklar sağlanabilir.
Belirli aşamada bir sürecin, mesela bir kimya sürecinin kontrolü için çeşitli işaretler kullanılabilir, `önce burada dur`, `şu göstergeyi kontrol et`, `sonra burada dur`, `burada şu değeri kaydet`, `sonra burada dur` şeklindeki komutlardan oluşan işaretler,
bir kontrol listesi ile karşılaştırılarak, süreç rahatlıkla ve hatasız olarak kontrol edilebilir. Süreci kontrol edenler bu bilgileri diğer kişilerle, diğer vardiya çalışanları ile kolaylıkla paylaşabilir.
Üçüncü aşama faaliyetler seiso` temizlemek anlamına gelir. Toz, çöp ve yabana maddeler çalışma ortamından uzaklaştırılmalı, bu işlemler pratik hale getirilmeli ve özenle yapılmalıdır.
Makina talaştan, eğelenen kırpıntılar, ve diğer artık maddeler, yerçekimi de kullanılarak, pratik bir şekilde temizlenir olmalıdır. Kenarlığı olmayan bir masada yapılan işlemler sonucu oluşan kirliliğin temizliği için zaman ve para harcamak gerekir. Oysa kenarlığı olan bir masaya bir delik açılıp, altına bir kutu konulduğunda temizlik için yapılan harcamalar en aza indirilerek avantaj elde edilebilir.
Aşağıdaki şekil diğer bir 5S Kaizen örneğidir. Değişik amaçlar için ortak olarak kullanılan süpürge ve paspaslar, boylarına göre asılabilir; böylece arandıkları zaman rahatlıkla bulunabilirler.
Dördüncü aşama `seiketsu` yani standardizasyon için öncelikle ideal durum tanımlanır. "Bu deponun ideal durumu nedir?" sorusunun cevabı, "Şu malzemeler şurada durur, böyle istiflenir, şu tür kutuları vardır, bunlar burada durur, iki taneden fazlası üst üste konulmamalıdır" gibi tanımlar içerebilir. Standardizasyon ile amaçlanan, tanımlanan ideal durum ile mevcut durum arasındaki farkı kapatmaktır.
Arızaları kolay tamir etmek için, bir kazan dairesinde giden boruları bir renge, dönen boruları başka bir renge boyamak, vanaların ne yöne açıldığını oklarla göstermek, göstergelerin limitlerini işaretlemek gibi derinlemesine faaliyetleri tanımlayıp diğer çalışanlara da öğretmek standardizasyonun temelini oluşturur.
Beşinci aşama `shitsuke` yani disiplin (otokontrol) yapılan iyileştirmelerin sürdürülebilirliğidir; 5S Kaizenler ile elde edilen çalışma ortamında ki düzelmelerin kalıcı olması gerekir. Kalıcılık disiplin kuralları ile paralel yürütülmeli ve kontrol edilmelidir. Oluşturulan disiplin, düzgün alışkanlıklar denetlenerek ve kontrol edilerek korunabilir.
Bu kurallar grubu iş kazalarını önlemeye yönelik olarak, sigara içmemek, içirmemek gibi disiplin faktörleri, güvenlik kuralları ve bu kurallara doğal olarak uymak önem taşır.
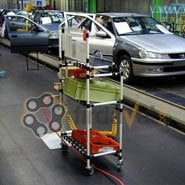
KOBETSU KAİZEN
Kobetsu Kaizen" ekipler tarafından yapılan Kaizenlerdir. Metodik şekilde önemli iyileşmeler sağlamak için Kobetsu Kaizenler yapılır. Hedef hataları sıfırlayıp, kaliteyi iyileştirmek, üretim ve teslim sürelerini kısaltmaktır. Kayıplar azaltılıp, fireler düşürülerek maliyeti düşürmek üzere yoğunlaşılır.
Kobetsu Kaizende daha bilinçli bir Kaizen sözkonusudur ve daha fazla eğitim gereklidir. Birçok durumda, çalışanların, kayıt ve istatistik tutmaları, grafik çizmeleri için bir ön eğitim almaları gerekebilir.
Hedef bir grup çalışanın çalışma bölgelerindeki hataları ekip çalışması yaparak sıfırlamaları, kaliteyi yükseltmeleridir.
Yapılacak olan iyileştirmelerde, "Muda" olarak adlandırılan 16 büyük kayıp referans alınabilir. Sağlanacak olan tüm bu iyileşmeler için bir hedef süre koymak gerekir.
Diğer "Kaizen"lerde olduğu gibi, bir üretim birimindeki problem, ilgili birimin kendisi tarafından bulunabilir. Örneğin boya bölümünde %10`luk bir kaybın nereden kaynaklandığını bulmak için, daha önce hangi operasyonlarda bu hataların oluştuğunun birim üyeleri tarafından analiz edilmesi gerekir. Yapılacak analizin yapıcı ve pozitif olması, suçlama şeklinde olmaması çok önemlidir. İşlem sırasında ters baskı hatası nedeniyle oluşacak boya ve işgücü kaybını engellemek için bir yöntem geliştirilebilir. Herhangi bir pozisyonda çıkan %10 hatayı geriye dönük iyileştirmelerle yoketmek, sıfıra indirmek için ekip bir müddet çalışır; ilgili aparat kullanımı revize edilebilir, başka bir makina ile değiştirilebilir, diğer düzenlemelerle metodoloji iyileştirilir ve netice tekrar ölçülür. Sonuçta, %10 hata oranın %2`ye indiği gözlenebilir. Bir sonraki Kaizen %2 hata oranını sıfıra indirmek ya da yaklaştırmak olabilir.
Kaizen yapabilmek için, model çalışma şekli belirlenir ve Kobetsu Kaizen formları hazırlanır. Kayıplar, hatalar, hataların oluştuğu yer, yapılan Kaizen ve sonuçları, hedefler bu formlarda yer alır. Gelişmeler işaretlenir, değiştirilir, Şekil 42`de bir Kobetzu Kaizen Formu içeriği görülmektedir.
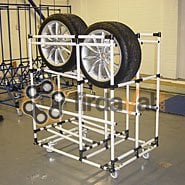
FABRİKALARDA 16 BÜYÜK KAYIP (Muda)
Fabrikalardaki kayıplar genellenmiş ve tanımlanmıştır. Aşağıda bu gruplanmış kayıp alanları vardır. Bu kayıp alanları yok edildiği takdirde fabrikaların verimi artar. Japonlar bu kayıplara "Muda" demektedir.
"Kaizen" açısından bakıldığında problem teşhisi için önceden belirlenmiş bu Standard alanların kullanımı düşünce, yönlendirme ve istatistikler açısından yararlıdır.
Ekipmanı verimsizleştiren 8 kayıp:
1) Arıza: Makinanın veya bir üretim hattının durmasına neden olan ve 3 dakikadan uzun süren duruşlardır.
2) İş bağlama, ayar (set-up): Model değişikliği ve/veya tezgahlara parça bağlama sırasındaoluşan ve ilk kaliteli ürün elde edilinceye kadar geçen süredir.
3) Takım, bıçak, aparat değişimi: Uzun kullanım sonucu kırılmış veya aşınmış bıçak, uç veya aparatların değiştirilmesi esnasında oluşan duruşlardır.
4) Başlangıç: Çalışmaya başlamadan önce özellikle ısınması yada rejime girmesi gereken ekipmanlarda ekipman ilk üretim için hazır olana dek geçen süredir. İşbaşı saatlerinin başlarında oluşan ve makinalardan ilk kaliteli ürünü elde edinceye kadar geçen tüm duruşlar da bu kapsamda değerlendirilebilir.
5) Küçük duruşlar ve boşta bekleme: Makinanın veya üretim hattının durmasına neden olan ve 3 dakikaya kadar olan duruşlardır.
6) Hız: Makinanın üretimde olan ürün için tesbit edilen hız yerine daha yavaş çalıştırılması ile oluşan kayıplardır.
7) Hatalı üretim ve tamir: Hatalı üretilen ürünün tamiri için harcanan süre, parça ve malzemelerdir.
8) Makina kapatma: Önceden bilinen tüm makina kapatmalarıdır (çay-yemek molaları, periyodik bakım, toplantılar, iş yokluğu v.s.).
İşgücünü verimsizleştiren 5 kayıp:
1) Yönetim: Geciken malzeme, takım, tamir ve talimat bekleme kayıplarıdır. Stok fazlası nedeni ile oluşan duruşlar da yönetim kaybıdır.
2) Üretim içi hareketler: Lüzumsuz mal hareketi, istif, istiften tekrar alma, operatörlerin yaptığı iş ile ilgili beceri eksikliğinden, hatalı malzemeden veya hatalı el aleti ve ekipmandan kaynaklı yavaşlamalardır.
3) Hat organizasyon hataları: Hat dengesinin bozulması nedeniyle tüm işlerin en yavaş tempoya düşmesi ile oluşan kayıplardır.
4) Lojistik: Fabrika içinde yapılan malzeme taşıma (lojistik) ile ilgili kişinin yapması gereken işi operatörün yapması nedeniyle oluşan duruşlardır.
5) Ölçme ve ayar: Hatalı ürün üretimini önlemek amacıyla sık tekrarlanan, lüzumsuz ölçme-ayar kayıplarıdır.
Malzeme ve enerji kayıpları:
1) Bozuk üretilmiş ürün oranı: Hatalı üretim nedeniyle atılan malzemelerin (kırık parçalar, hammadde ve malzemeler v.s.) maliyet kaybıdır.
2) Enerji (lüzumsuz ve fazla kullanım): Makinanın üretim yapmadığı zaman fazladan harcanan ısı, ışık, elektrik, hava ve suyun getirdiği ekstra maliyettir.
3) Kalıplar, el aletleri, aparatlar: Kullanım dışı olan, lüzumsuz yedek parça, kalıp, aparat v.s. maliyet kaybıdır.
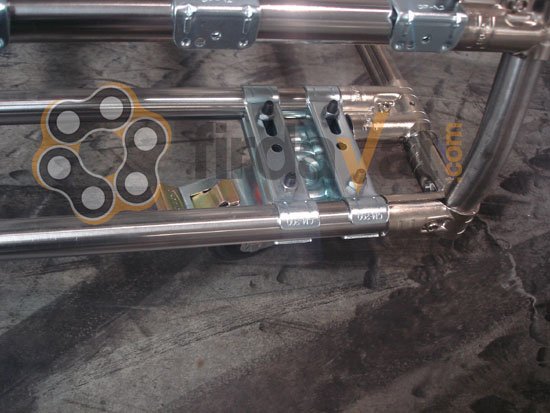
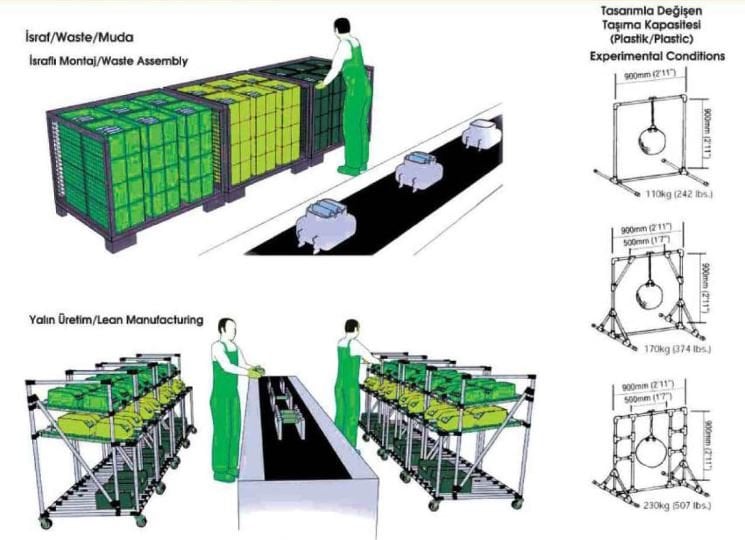
