كايزن و5S
ما هو الكايزن؟ ما هو ليس كذلك؟
بالإضافة إلى المساهمة الكبيرة للإدارة في تطوير المصانع، فمن الواضح أن العديد من التحسينات ("كايزن") التي تم إجراؤها من خلال تشجيع الإبداع لدى جميع الموظفين ستقدم مساهمة كبيرة في منتجاتنا وعمليات الإنتاج وبالتالي قدرتنا التنافسية.
في اليابانية، تعني كلمة "Kai" "التغيير" وكلمة "Zen" تعني "جيد، أفضل". كايزن هي كلمة يابانية تعني "التحسين المستمر". الفكرة الرئيسية لـ Kaizen هي أن الأشخاص، كفريق أو بشكل فردي، يجدون باستمرار وينفذون تحسينات صغيرة في بيئتهم وفي المجالات التي يتحملون مسؤوليتها.
وبطريقة مختلفة تمامًا، الابتكار هو التغيير الجذري للوضع الحالي نتيجة للتغييرات و/أو الاستثمارات الكبرى التي تمت في التكنولوجيا و/أو الأدوات الجديدة، وهذا ليس كايزن.
بالنسبة للكايزن، من الضروري عدم الرضا عن الظروف والمعايير الحالية التي تم تحقيقها بالفعل، ولكن البحث عن الابتكارات والفخر وتقدير التحسينات التي تم إجراؤها. بداية التحسين هي الاعتراف بالحاجة إلى التحسين. تنشأ الحاجة عندما يتم التعرف على مشكلة أو عدم كفاية المعيار. الأشخاص الذين يحتاجون إلى إدراك هذه المشكلات هم أولئك الذين يقومون بالعمل بأنفسهم. إذا لم تكن هناك مشكلة ملحوظة، فلا داعي للتحسين، وبالتالي لا يمكن خلق الجو اللازم لكايزن.
الكايزن ينفذه من؟
يغطي كايزن جميع الموظفين في المصنع. ومن خلال تشجيع الموظفين يمكن تنفيذ العديد من الكايزن من قبل الأفراد والحصول على نتائج فعالة، وهذا أمر مهم للغاية. من ناحية أخرى، في المصانع المتوسطة والكبيرة الحجم، يمكن القيام بالعمل الجماعي من قبل أشخاص ذوي مسؤوليات مختلفة، باستخدام تقنيات حل المشكلات، بسبب تقسيم العمل. تُستخدم تقنيات حل المشكلات أيضًا على نطاق واسع في أعمال الفريق هذه. أعمال التحسين المنهجية التي تقوم بها الفرق تسمى "كوبيتسو كايزن".
في أي المجالات يمكن تطبيق الكايزن؟
يمكن تطبيق كايزن على المنتجات وعمليات الإنتاج في أماكن العمل، في المكتب، في المنزل، في المستشفى، باختصار، في أي مكان وفي أي وقت. في اليابان على وجه الخصوص، يتم تطبيق كايزن في جميع مجالات الحياة. من خلال تنفيذ Kaizens في المصانع بما يتماشى مع هدف تقليل 16 خسارة كبيرة، تسمى "Muda" باللغة اليابانية، إلى الصفر، يمكن زيادة الإنتاجية وتحقيق تخفيضات كبيرة في تكاليف المنتج والإنتاج.
وفي واقع الأمر، فإن الموظفين في العديد من المصانع التي تم فيها تطبيق ممارسات كايزن قد طوروا قدراتهم الإبداعية، واستخدموا الابتكارات التي ابتكروها، وارتقوا إلى مكانة رائدة تليها شركات أخرى من خلال التحسين المستمر لآلاتهم ومجالات عملهم ومنتجاتهم. وكانت الانطباعات الإيجابية للجمهور الذي حضر العروض التي قدمها موظفو المصنع مؤشرا على هذا التطور.
في البيئة التنافسية الحالية، من المهم جدًا مدى جودة تنفيذ العملية عند تحويل المدخلات إلى منتجات. لأن العملاء يشترون المنتج الصناعي من خلال مقارنة "معايير القيمة" المعروفة بـ "الجودة، التكلفة، وقت التسليم" مع سعر المنتج.
QCD: الأحرف الأولى باللغة الإنجليزية من الكلمات الجودة والتكلفة ووقت التسليم.
"يحتاج المنتجون إلى زيادة معايير القيمة في المخرجات من أجل بيع المزيد من منتجاتهم. يمكن أن تكون هذه الزيادة ممكنة من خلال النظر في تصميم المنتج وعمليات الإنتاج وعوامل 5M.
الفرق الذي تم إنشاؤه للعميل يحدد المنافسة. ولذلك، فإن الفرق يكمن في التحسين والانتعاش السريع واكتساب القدرة التنافسية من خلال تلبية معايير القيمة الخاصة بالعميل بشكل أفضل.
كلمة كايزن تتكون من الكلمتين اليابانيتين "Kai" و"Zen" وتعني "التحسين المستمر". الفكرة الرئيسية لـ Kaizen هي البحث المستمر عن تحسينات صغيرة وتنفيذها في بيئة الفرد وفي المجالات التي يكون الشخص مسؤولاً عنها، سواء كفريق أو كفرد.
في الصناعة، تعتبر العمليات والمخرجات مهمة في إحداث الفرق. هذه هي المخرجات التي يتم إنتاجها من خلال مراعاة الجودة والتكلفة ووقت التسليم. من الممكن تحسين العمليات الصناعية بشكل كبير من خلال أنشطة كايزن التي يتم تنفيذها يوميًا. ولذلك، تنخفض التكاليف، وتزيد الجودة، ويقصر وقت التسليم. ولذلك فإن كايزن هي الأنشطة التي تعمل على تحسين معايير القيمة في المخرجات مع تحسينات طفيفة في العمليات.
كايزن، كما عرفتها الموارد البشرية اليابانية، هي مجموعة من التحسينات أو تغيير الطريقة المستخدمة لغرض ما. تعريف آخر هو التحسينات التي يتم إجراؤها من خلال تراكم التغييرات الصغيرة. ولذلك، فإن كايزن هو ما يمكن لأي شخص أن يفعله، وهو ما فعلوه في ذلك اليوم! وهي التحسينات التي يمكن أن يقوم بها الشخص الذي يعرف الوظيفة بشكل أفضل ويعمل على المنضدة، واستمراريتها من خلال إجرائها بأعداد كبيرة.
فيما يتعلق بالصناعة، فإن كايزن هو تحسين الإنتاج عن طريق إجراء تغييرات صغيرة في طريقة الإنتاج - العملية أو العمليات - ميزات المنتج لغرض ما.
على سبيل المثال، يمكن للتحسين الذي يجريه عامل يعمل في صناعة الملابس أن يوفر الوقت. كايزن هو تحسين صغير يقوم به المشغل في عمليته الخاصة، أي في طريقة الإنتاج أو في المنتجات المنتجة.
يمكن أيضًا تنفيذ Kaizens في ميزات المنتج.
بشكل أساسي، يعتبر تطبيق Kaizens على العمليات أكثر فعالية. عندما تتكرر العمليات كثيرًا في الإنتاج، يمكن تحقيق مستوى عالٍ من التحسين من خلال مجموع التحسينات الصغيرة في العملية التي تتكرر مئات أو آلاف المرات.
على سبيل المثال، لنفترض أن أحد المشغلين قام بتحسين بنسبة 7% في عمليته مع كايزن. في هذه الحالة، يمكن الحصول على منتج فائض قدره 70 قطعة في دفعة إنتاج مكونة من 1000 قطعة.
يمكن تحقيق الكايزن بميزانية حالية متواضعة، وموظفين موجودين، ومعدات وآلات موجودة.
أولاً، دعونا نتحدث عن "كايزن" قبل وبعد، والذي نعرّفه بأنه تحسين الأسلوب باستخدام الأفكار والدراسات الفردية. أبسط مثال يمكن أن يكون كما يلي: على سبيل المثال، لنفترض أن شخصين، أحدهما قصير والآخر طويل القامة، يعملان معًا على طاولة العمل. يمكن لأحد الموظفين القيام بكايزن: يمكن مساعدة الشخص القصير على الارتقاء بنفسه من خلال وضع منصة تحت قدميه. وبهذه الطريقة، يتم تحقيق تحسن في العملية، ويمكن إنجاز العمل بسهولة أكبر، ونتيجة لذلك، تزداد الكفاءة.
أولاً: لنأخذ بعين الاعتبار بيئة العمل التي يتم فيها تنظيف نتوءات الجزء المعدني. سطح الطاولة مليء بالغبار المعدني، الذي يسقط على الأرض، ومن وقت لآخر ينسكب على الأرض، ثم يتم تنظيفه. وطبعا مجهود ضائع وخسارة ضائعة..
بعد: يمكن للموظف أن يفعل ثلاثة كايزن: أولاً، يصنع درعًا على حافة مكتبه لمنع تساقط الغبار على الأرض؛ وبهذه الطريقة يتجنب أولاً اتساخ المكان ومن ثم تنظيفه دون جدوى. وبعد ذلك الكايزن الثاني: إذا حفرنا حفرة في الطاولة ووضعنا تحتها صندوق نشارة، أليس ذلك أسهل من تنظيف نشارة الخشب من الطاولة بشكل متكرر؟ قد يكون من الضروري سكب سلة نشارة الخشب فقط عندما تكون ممتلئة. الكايزن الثالث: لماذا يجب أن ننحني تحت الطاولة ونلتقط صندوق النشارة ونحمله باليد؟ إذا وضعنا عربة بعجلات أسفل صندوق نشارة الخشب بدلاً من ذلك، فيمكننا بسهولة أخذها إلى أي مكان نريده عندما يكون ممتلئًا.
زر التشغيل والإيقاف لآلة موازنة الإطارات مكسور بسبب الاستخدام المتكرر. يقوم المشغل بإصلاح الجزء المكسور من زر التشغيل والإيقاف بشريط ويمنع التلوث المستمر. يتم استبدال قطعة الشريط التي تتسخ من وقت لآخر.
كيف نفعل كايزن؟
ولإجراء تحسينات، يتم أولاً تحديد المشكلة، ثم يتم توليد الأفكار وتحديد اقتراحات الحلول. وأخيراً تم تنفيذ التوصيات. الفكرة التي لا يتم تنفيذها ليس لها معنى، أي أن الشفاء لا يحدث.
في مرحلة تحديد المشكلة؛ إذا كان يُعتقد أن "ما يتم إنجازه حاليًا هو الأفضل"، فقد لا يكون من الممكن تحسين ما يتم إنجازه.
طرق إيجاد المشكلة
الطريقة الأولى؛ هو ملاحظة المشاكل المرئية مثل المشاكل والأخطاء والأخطاء والمتاعب. على سبيل المثال، قد يعتقد الموظف أن "الآلات تبدو مختلفة اليوم". إذا تغير صوت الجهاز، فهناك مشكلة قادمة. يشعر هذا الموظف بالمشكلة ويبلغ عن هذا الموقف إلى رئيس العمال أو الرئيس أو المشرف أو رئيس الورشة أو المدير. يمكن للموظفين الذين يمكنهم الشعور بمثل هذه المواقف أيضًا تولي أدوار قيادية داخل نظام كايزن.
هناك أيضًا مشاكل غير مرئية. حتى لو لم تكن هناك مشكلة في العمليات، فقد تكون هناك بعض الخسائر.
وفي نهاية الكتاب، تم إدراج 16 خسارة كبرى، أطلق عليها اليابانيون اسم "مودا"، والتي يمكن استخدامها للتعرف على هذه المشاكل. هذه هي 8 خسائر تجعل المعدات غير فعالة، و 5 خسائر تقلل من كفاءة العمل، و خسائر المواد والطاقة. هذه الخسائر الـ 16 هي خسائر متكبدة في المصانع. لذلك، سواء كان ذلك مكاتب هندسية أو مدراء أو موظفين،
إذا تم التركيز على هذه الخسائر الـ 16، فيمكن القيام بالعديد من الكايزين لتقليل الخسائر. ومن بين المشاكل غير المرئية، إهدار الحركات والخدمات اللوجستية من بين الخسائر الـ 16. هناك أيضًا خسائر جزئية بسبب أخطاء في تنظيم الخط. عندما يتعلق الأمر بالمعدات، فإن فقدان السرعة يعد خسارة مماثلة.
من أجل العثور على هذه المشاكل وتحديد موقعها، من الضروري التفكير باستخدام بعض الكلمات الرئيسية مثل "لماذا" و"ماذا حدث". "إنه دائما مثل هذا." "لماذا؟ أنا لا أريد أن يكون الأمر بهذه الطريقة، يمكن أن يكون أفضل." الأفكار مثل "هناك خطأ ما هنا" هي في الواقع بيانات للتحسينات. بدلاً من التفكير في أن أشخاصًا محددين فقط يمكنهم إجراء التحسينات، يجب عليك التشكيك في هذا الموقف وتذكر أنه قد يكون هناك موظفون آخرون في الشركة سيقومون بإجراء التحسينات اللازمة. ولذلك، فإن هذه الكلمات الرئيسية هي الكلمات التي تثير منطق التفكير هذا.
المرحلة الثانية: توليد الفكرة. من الضروري توليد الأفكار لحل المشكلة. أثناء توليد الأفكار، يتم تحفيز الكايزين من خلال طريقة الحذف والتخفيض والاستبدال. ما هو غير ضروري يمكن التخلص منه. يمكن تحقيق كايزن عن طريق تقليل ما هو غير ضروري. هذه تحسينات على المنتجات التي تقلل الإنتاج. أو يمكن تحقيق الكايزن عن طريق تغييره. ولذلك، يمكن توليد الأفكار في هذه المجالات الثلاثة.
مثال آخر لشرح تطبيق "كايزن بالتغيير" هو مراوح التبريد الخاصة بلوحات التحكم في المصانع. غالبًا ما يؤدي فشل المراوح في اللوحة الكهربائية بالمصنع إلى تعطل الأجهزة. ولذلك، فمن الضروري التأكد من أن المشجعين يعملون. الاستماع إلى ضجيج المروحة ليس الطريقة الوحيدة. الطريقة الموضحة أدناه هي طريقة عملية مطبقة في العديد من المصانع. يتم ربط الشريط بشبكات المراوح، نظرًا لأن الأشرطة سوف تموج أثناء تشغيل المراوح، فمن السهل أن نفهم حتى من مسافة ما إذا كانت المراوح تعمل أم لا. إذا لم يتم تهوية الأشرطة، فهذا يشير إلى أن المراوح لا تعمل ويجب استبدالها.
يقوم الضاغط الموجود في زاوية الورشة بتبريد نفسه عن طريق سحب الهواء الموجود داخل الورشة ويتم رمي الهواء الدافئ الناتج إلى السماء من خلال قناة. في فصل الشتاء، يشعر الموظفون أحيانًا بالبرد عند فتح الباب في مكان قريب، ويوصون بوضع مدافئ كهربائية في هذه المرحلة. قام رجل الصيانة بالمصنع بإجراء كايزن وقام بسد مسار خروج الهواء الساخن بقطعة من الصاج وفتح فتحة بجوار مجرى الهواء الساخن باتجاه الورشة. وبالتالي، يتم استخدام الهواء الساخن المهدور لتدفئة الورشة، وبالتالي توفير احتياجات التدفئة للموظفين. في الصيف، سيتم إغلاق الفتحة المؤدية إلى ورشة العمل، وستتم إزالة قطعة الصفائح المعدنية التي تسد فتحة القناة وسيتم إطلاق الهواء الساخن مرة أخرى. وبالتالي، لا تحتاج الشركة إلى شراء ما يقرب من 3000 سعر حراري/ساعة من الطاقة الإضافية.
5S كايزن
إذا كان الكمال التام مطلوبًا في بيئة العمل، فيمكن تحسين تخطيط المصنع وورشة العمل بشكل منهجي باستخدام 5S Kaizens. "5S Kaizen" هو تحسين بيئة العمل من خلال الأنشطة الفردية و/أو الجماعية.
وفي المصانع والورش العادية تقف الأدوات والأدوات في أماكنها، وتوجد الآلات بجوار المكان الذي تقف فيه الأدوات. حتى لو كانت الأرضيات قديمة، فهي نظيفة، وهناك دلاء وصناديق منفصلة حيث يتم جمع القصاصات ونشارة الخشب والقصاصات. وفي مثل هذه المصانع تكون الكفاءة عالية والتكاليف منخفضة والنفايات منخفضة وتحت السيطرة والعيوب في المنتجات قليلة.
في بعض الأحيان قد لا يكون هذا الطلب موجودًا في جميع ورش المصانع. قد تكون إحدى ورش العمل غير منظمة، وغير فعالة، ولها بيئة عمل رديئة الجودة مما يؤدي إلى تعطيل سير العمل وإبطائه. هناك احتمال كبير لحدوث اضطرابات في سير العمل بسبب البيئة غير النظامية. العديد من المشكلات التي لم يتم تسجيلها ولا يمكن قياسها ناتجة عن بيئة العمل السيئة.
وبما أن المنهجية انتشرت من اليابان وأصبحت هذه الكلمات رموزًا، فإن 5S تتكون من الأحرف الأولى من الكلمات اليابانية -seiri، seiton، seiso، seiketsu، Shitsuke. 5S تتكون من كلمات Recovery أو Order أو النظافة أو التقييس أو الانضباط أو Self-. يتحكم. .
هنا، من الممكن التحسين التدريجي لقضايا التعافي والنظام والنظافة والتوحيد والانضباط، أي كايزن.
55 المرحلة الأولى من Kaizens هي "seiri"، أي التعافي. أول شيء يجب القيام به في منطقة العمل هو التعافي في 5S Kaizens.
بداية، يمكننا أن نبدأ بتحديد وتمييز ما هو ضروري وما هو غير ضروري في الإنتاج وتنظيف ما هو غير ضروري. لا ينبغي الاحتفاظ بالمواد أو الأدوات أو الأجهزة التي لا تستخدم في عمليات الإنتاج في بيئة العمل.
أثناء مرحلة الترتيب، يوصى في البداية بالتقاط صورة للمكان الفوضوي حتى يمكن ملاحظة الفرق وخلق الوعي. إظهار الفرق بين قبل وبعد ومشاركة الموظفين الفخر بالتحسين الذي تم إجراؤه،
ويمكن استخدامه كأداة تحفيزية مهمة لنشر كايزن.
وفي طريقة عملية أخرى يستخدمها المصنعون اليابانيون، عندما يبدأ المشغل العمل في الأول من الشهر، فإنه يضع علامة حمراء على الفولاذ والأدوات والآلات وجميع المواد والمعدات الموجودة في البيئة التي يعمل فيها. يرمي الملصقات الموجودة على المواد والأدوات والأجهزة التي استخدمها خلال الشهر. وفي نهاية الشهر، يقوم بفحص المواد والأدوات التي لا تزال عليها ملصقات حمراء؛ وبالتالي فهو يحدد المواد التي لا يستخدمها لمدة شهر. في معظم الأحيان، لا يدرك الموظفون حتى أن هذه الأدوات أو الأجهزة موجودة بالفعل. يمكن إعطاء الجهاز الذي لم يتم استخدامه لمدة شهر لشخص آخر أو لوحدة أخرى لاستخدامه في عملية أخرى.
وبهذه الطريقة، يتم الكشف عن المواد أو الأدوات أو الأجهزة غير الضرورية والتي نادرًا ما تستخدم، وتحديدها. وبعد هذا التحديد يقرر تخزينها، أو إعادتها، أو بيعها، أو التخلص منها إذا كان سيتم تخريدها، وإخراجها من بيئة العمل. وبالتالي، تتوسع بيئة العمل، وعلى المدى الطويل، يمكن إنتاج المزيد من الإنتاج في نفس المتر المربع. نظرًا لوجود عدد أقل من المكونات حولك، يصبح من الأسهل اختيار المكونات والوصول إليها. والنتيجة هي زيادة الكفاءة.
النشاط الثاني "seiton" هو أن يكون منتظمًا. إن تكديس الأدوات بانتظام هو منعها من الضياع. الترتيب - seiri - والترتيب - seiton - يكمل كل منهما الآخر. أولاً، يتم التخلص من العناصر غير الضرورية من خلال عملية البطاقة الحمراء، ثم يتم تنظيمها وبالتالي يمكن تحقيق مكان عمل أفضل بسهولة.
يمكن العثور على الأداة أو الجهاز الذي قد تكون هناك حاجة إليه في نقطة الإنتاج خلال 30 ثانية على أبعد تقدير.
إن القدرة على العثور عليه هو شرط لتكون قادرًا على القيام بالمهمة بكفاءة دون انقطاع. وفقًا لـ "مبدأ الثلاثين ثانية"، يجب ألا تقضي أكثر من 30 ثانية للعثور على المادة التي سيتم استخدامها. على سبيل المثال، هذه المشكلة شائعة في عمليات تغيير القالب. توجد مكبس حقن بلاستيك أو مكبس غريب الأطوار في مكان ما وسيتم إرفاق القالب به. يتم إحضار القالب. مطلوب مفتاح ربط رقم 23 أولاً للمسامير التي تربط القالب بالطاولة. تم العثور على المفتاح رقم 23 وإحضاره، وتم تثبيت المزلاج. ومع ذلك، فإن المفتاح رقم 18 مطلوب أيضًا لنفس الوظيفة، ولكن هذا المفتاح غير موجود. لذلك، يتم تمديد وقت "الإعداد" للعملية بسبب ربط القالب؛ يتم حظر الصحافة لفترة أطول، ويتوقف ويفقد الإنتاج.
إذا كان المفتاح مفقودًا أو مفقودًا، فيجب ملاحظة ذلك منذ البداية، أي قبل عملية ربط القالب. بفضل النظام الموجود في الصورة، يمكن تحقيق ذلك من خلال الحفاظ على الأدوات في مكانها. الشيء المهم هو أن تكون قادرًا على العثور على المعدات التي سيتم استخدامها لوظيفة ما خلال 30 ثانية على الأكثر. وهذا هو أحد الأهداف الرئيسية لأنشطة 5S.
لذلك، يجب تنفيذ عمليات البحث والعثور هذه بطريقة عملية للغاية. على سبيل المثال، فإن تحديد موقع كل أداة بشكل واضح على اللوحات التي تم تعليق الأدوات اليدوية فيها يوفر فوائد كبيرة لأخذ الأدوات المفقودة وإعادتها وتحديدها والبحث عنها قبل فقدانها.
ونتيجة لذلك، يمكن تحقيق التحسين من خلال أن تكون أكثر وظيفية في تصميم التخطيط والعمل مع أجزاء محددة.
لا يمكن إنكار سهولة وفائدة العثور على المواد المطلوبة عند الحاجة إليها، والتي يتم الحصول عليها من خلال مجموعة مرتبة جيدًا. ومن أجل القضاء على مثل هذه الخسائر، تعتبر أنشطة "السيتون" والأماكن التي يتم فيها فصل المواد الخام وإحاطتها بالخطوط مهمة وضرورية للغاية.
من حيث المبدأ، يعد الاتساق بين الرموز الموجودة على الرف والرموز الموجودة على الأجزاء عاملاً مهمًا لتوفير الوقت. يجب أن يتم تصنيف المواد حسب أنواعها وأن تكون أماكن الصناديق التي تحتوي على هذه المواد واضحة.
إحدى الطرق المفيدة في هذا الصدد هي مطابقة النص الموجود على صندوق المواد مع النص الموجود على الرف. بهذه الطريقة، يمكن تحقيق راحة كبيرة في التنسيب والعثور.
يمكن استخدام إشارات مختلفة للتحكم في عملية ما في مرحلة معينة، على سبيل المثال عملية كيميائية، إشارات تتكون من أوامر مثل "توقف هنا أولاً"، "تحقق من هذا المؤشر"، "توقف هنا لاحقًا"، "سجل هذه القيمة هنا" "توقف هنا لاحقا"
ومن خلال مقارنتها بقائمة مرجعية، يمكن التحكم في العملية بسهولة ودون أخطاء. يمكن لأولئك الذين يتحكمون في العملية مشاركة هذه المعلومات بسهولة مع أشخاص آخرين وعمال المناوبة الآخرين.
أنشطة المرحلة الثالثة seiso` تعني المقاصة. يجب إزالة الغبار والقمامة والمواد الغريبة من بيئة العمل، ويجب أن تكون هذه العمليات عملية ويتم تنفيذها بعناية.
يجب أن تكون الآلة قادرة على تنظيف نشارة الخشب والقصاصات وغيرها من المخلفات بطريقة عملية، وذلك باستخدام الجاذبية أيضًا. من الضروري إنفاق الوقت والمال لتنظيف التلوث الناتج عن العمليات التي تتم على طاولة بلا حدود. ومع ذلك، عندما يتم حفر ثقب في طاولة ذات إطار ويتم وضع صندوق أسفلها، يمكن تقليل تكاليف التنظيف ويمكن الحصول على ميزة.
الشكل أدناه هو مثال آخر لكايزن 5S. يمكن تعليق المكانس والمماسح شائعة الاستخدام لأغراض مختلفة وفقًا لطولها؛ بحيث يمكن العثور عليها بسهولة عند البحث عنها.
بالنسبة للمرحلة الرابعة، "seiketsu"، أي التوحيد القياسي، يتم أولاً تحديد الوضع المثالي. "ما هو الوضع المثالي لهذا المستودع؟" قد تتضمن إجابة السؤال تعريفات مثل "توضع هذه المواد هنا، وهي مكدسة هكذا، ولها مثل هذه الصناديق، وتوضع هنا، ولا يجوز وضع أكثر من اثنتين فوق بعضها البعض". الهدف من التقييس هو سد الفجوة بين الوضع المثالي المحدد والوضع الحالي.
من أجل إصلاح الأعطال بسهولة، تعريف وتعليم أنشطة متعمقة للموظفين الآخرين، مثل طلاء الأنابيب الخارجة في غرفة الغلاية بلون واحد والأنابيب العائدة بلون آخر، مع إظهار الأسهم في اتجاه فتح الصمامات، ووضع علامات حدود المؤشرات تشكل أساس التقييس.
المرحلة الخامسة هي "shitsuke"، أي الانضباط (ضبط النفس) واستدامة التحسينات التي تم إجراؤها؛ يجب أن تكون التحسينات التي يتم تحقيقها في بيئة العمل من خلال 5S Kaizens دائمة. يجب أن يتم تنفيذ الدوام ومراقبته بالتوازي مع القواعد التأديبية. يمكن الحفاظ على الانضباط الراسخ من خلال مراقبة العادات الجيدة والتحكم فيها.
من أجل منع حوادث العمل في هذه المجموعة من القواعد، تعتبر العوامل التأديبية مثل عدم التدخين أو عدم السماح بالكحول وقواعد السلامة والامتثال الطبيعي لهذه القواعد مهمة.
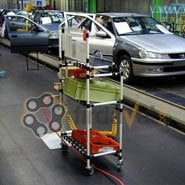
كوبيتسو كايزن
"Kobetsu Kaizen" هي عمليات Kaizen يتم تنفيذها بواسطة فرق من أجل تحقيق تحسينات كبيرة بطريقة منهجية والهدف هو إعادة ضبط الأخطاء وتحسين الجودة وتقصير أوقات الإنتاج والتسليم تقليل الخسائر والهدر.
في كوبيتسو كايزن، هناك كايزن أكثر وعيًا ويتطلب المزيد من التدريب. في كثير من الحالات، قد يحتاج الموظفون إلى تلقي تدريب أولي للاحتفاظ بالسجلات والإحصاءات ورسم الرسوم البيانية.
الهدف هو أن تقوم مجموعة من الموظفين بإزالة الأخطاء في مجالات عملهم من خلال العمل كفريق وتحسين الجودة.
في التحسينات التي سيتم إجراؤها، يمكن اعتبار 16 خسارة كبيرة تسمى "Muda" كمرجع. ومن الضروري تحديد وقت مستهدف لتحقيق كل هذه التحسينات.
كما هو الحال في "كايزن" الأخرى، يمكن العثور على المشكلة في وحدة الإنتاج من خلال الوحدة ذات الصلة نفسها. على سبيل المثال، من أجل معرفة مصدر الخسارة بنسبة 10% في قسم الطلاء، يجب على أعضاء الوحدة تحليل العمليات التي حدثت فيها هذه الأخطاء من قبل. ومن المهم جداً أن يكون التحليل الذي سيتم إجراؤه بناءاً وإيجابياً، وليس على شكل اتهامات. يمكن تطوير طريقة لمنع فقدان الحبر والعمالة بسبب أخطاء الطباعة العكسية أثناء العملية. يعمل الفريق لفترة من الوقت على إزالة الخطأ بنسبة 10% في أي منصب من خلال التحسينات بأثر رجعي وتقليصه إلى الصفر؛ يمكن مراجعة استخدام الأجهزة ذات الصلة، واستبدالها بجهاز آخر، ويمكن تحسين المنهجية بترتيبات أخرى، ويتم قياس النتيجة مرة أخرى. ونتيجة لذلك يمكن ملاحظة انخفاض معدل الخطأ من 10% إلى 2%. قد يكون الكايزن التالي هو تقليل معدل الخطأ بنسبة 2% إلى الصفر أو بالقرب منه.
من أجل تنفيذ كايزن، يتم تحديد أسلوب العمل النموذجي وإعداد نماذج كوبيتسو كايزن. يتم تضمين الخسائر والأخطاء ومكان حدوث الأخطاء وأداء كايزن ونتائجه والأهداف في هذه النماذج. تم وضع علامة على التطورات وتغييرها ويبين الشكل 42 محتوى نموذج كوبيتسو كايزن.
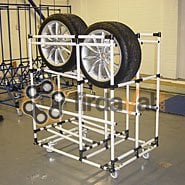
16 خسارة كبيرة في المصانع (مودا)
يتم تعميم وتحديد الخسائر في المصانع. فيما يلي مناطق الخسارة المجمعة هذه. وإذا تم التخلص من مناطق الخسارة هذه، تزداد كفاءة المصانع. يطلق اليابانيون على هذه الخسائر اسم "مودا".
من منظور "كايزن"، يعد استخدام هذه المجالات القياسية المحددة مسبقًا لتشخيص المشكلات مفيدًا من حيث التفكير والتوجيه والإحصائيات.
8 خسائر تجعل المعدات غير فعالة:
1) العطل: التوقف الذي يؤدي إلى توقف الآلة أو خط الإنتاج لمدة تزيد عن 3 دقائق.
2) الإعداد: هي الفترة الزمنية التي تحدث أثناء تغيير النموذج و/أو تركيب الأجزاء على المقاعد وحتى الحصول على المنتج عالي الجودة.
3) تغيير الأدوات والشفرات والأجهزة: وهي فترات التوقف التي تحدث أثناء استبدال الشفرات أو الأطراف أو الأجهزة التي تتعرض للكسر أو التآكل نتيجة الاستخدام الطويل.
4) بدء التشغيل: هي الفترة التي تصبح فيها المعدات جاهزة للإنتاج الأول، خاصة في المعدات التي تحتاج إلى إحماء أو دخول النظام قبل البدء في العمل. يمكن أيضًا تقييم جميع فترات التوقف التي تحدث في بداية ساعات العمل حتى يتم الحصول على المنتج عالي الجودة من الآلات في هذا السياق.
5) التوقفات البسيطة والانتظار الخامل: وهي فترات توقف تصل إلى 3 دقائق وتتسبب في توقف الآلة أو خط الإنتاج.
6) السرعة: الخسائر الناجمة عن تشغيل الآلة بشكل أبطأ من السرعة المحددة للمنتج في الإنتاج.
7) الإنتاج والإصلاح المعيب: الوقت والأجزاء والمواد التي يتم إنفاقها لإصلاح المنتج المعيب.
8) إيقاف تشغيل الآلة: جميع حالات إيقاف تشغيل الآلة المعروفة سابقاً (استراحات غداء الشاي، الصيانة الدورية، الاجتماعات، الغياب عن العمل، إلخ).
5 خسائر تجعل القوى العاملة غير فعالة:
1) الإدارة: فقدان انتظار المواد والأدوات والإصلاحات والتعليمات المتأخرة. فترات التوقف عن العمل الناجمة عن فائض المخزون هي أيضا خسائر إدارية.
2) الحركات أثناء الإنتاج: حركات البضائع غير الضرورية، والتكديس، وإعادة الأخذ من المكدس، والتباطؤ الناجم عن افتقار المشغلين إلى المهارة في العمل المنجز، أو المواد المعيبة أو الأدوات والمعدات اليدوية المعيبة.
3) أخطاء تنظيم الخط: هذه هي الخسائر التي تحدث عندما ينخفض كل العمل إلى أبطأ وتيرة بسبب اختلال توازن الخط.
4) الخدمات اللوجستية: هي فترات التوقف التي تحدث بسبب قيام المشغل بالعمل الذي يجب أن يقوم به الشخص المشارك في نقل المواد (اللوجستيات) داخل المصنع.
5) القياس والتعديل: هذه هي خسائر ضبط القياس غير الضرورية التي تتكرر بشكل متكرر من أجل منع إنتاج المنتج الخاطئ.
خسائر المواد والطاقة:
1) نسبة المنتج المعيب: هي خسارة تكلفة المواد (الأجزاء المكسورة والمواد الخام والمواد وما إلى ذلك) التي تم التخلص منها بسبب الإنتاج الخاطئ.
2) الطاقة (الاستخدام غير الضروري والمفرط): هي التكلفة الإضافية للحرارة والضوء والكهرباء والهواء والماء التي يتم صرفها عندما لا تكون الآلة قادرة على الإنتاج.
3) القوالب والأدوات اليدوية والأجهزة: تعتبر قطع الغيار والقوالب والأجهزة وغيرها غير الضرورية التي أصبحت غير صالحة للاستخدام بمثابة خسارة في التكلفة.
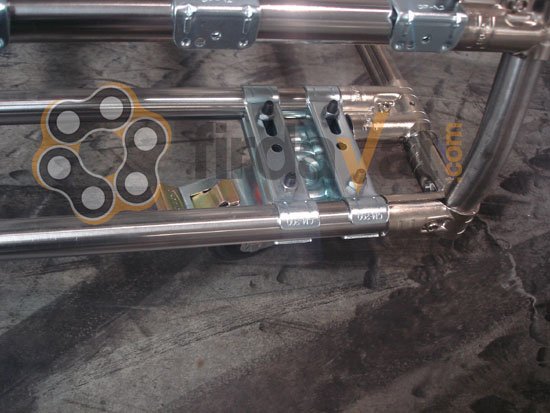
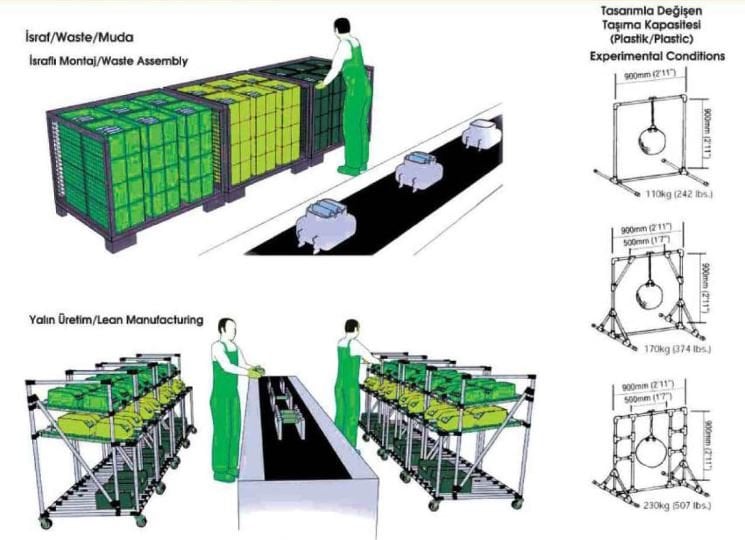
